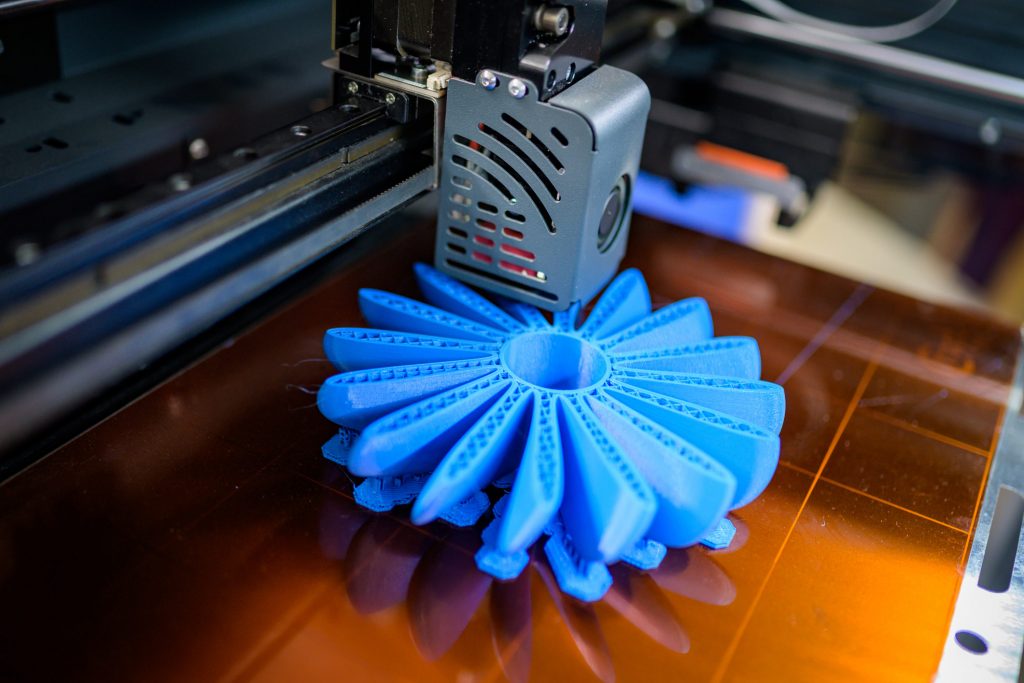
Fused Filament Fabrication bei fertig+
Das Fused Filament Fabrication (FFF) ist die weltweit verbreitetste Technologie zur Erstellung von Modellen aus Kunststoffen. Das Verfahren ist für die Fertigung von Prototypen ebenso geeignet wie für die Kleinserienproduktion.
Im Einsatz haben wir dabei unterschiedliche Systeme, die je nach Anwendungsfall gewählt werden. Der Einsatz unserer Printfarm bietet sich insbesondere an, wenn Ihre vorhandenen FFF/FDM Kapazitäten nicht ausreichend sein sollten.
Materialien im FFF
Die meisten der im FFF/FDM Verfahren angebotenen Materialien sind durch die Zugabe von Additiven optimiert. So kann eine problemlose Verarbeitung und gute Eigenschaften meist die des Originalmaterials übertreffen.
- UV-beständig
- exzellente mechanische Eigenschaften
- Hohe Hitzeresistenz (<105 °C)
- Unsere Empfehlung als Alternative zum ABS
Einsatzgebiete:
Bauteile, Gehäuse, Halterungen mit Anforderungen an einen hohen UV Schutz bei Außenanwendungen
- hohe chemische Beständigkeit
- Brandschutzzertifikat UL94 – V2
- in vielen Farben verfügbar
Das von uns genutzte PETG ist zu 100% recycelbar und trägt sogar den Recycling Code 1.
Das Filament hat ein vielfäliges Einsatzgebiet und es bietet hervorragende mechanische und optische Eigenschaften. Das verwendete Harz im Filament ist sehr hart. Es erfüllt auch die Anforderung der Europäischen Verordnung für Kunststoffe mit Lebensmittelkontakt und Arzneiprodukten.
Es ist eine transparente Variante verfügbar.
Eine mechanische Nachbearbeitung ist problemlos möglich, das Kleben gestaltet sich jedoch anspruchsvoll.
Das Material eignet sich daher für zahlreiche Anwendungen im Bereich der Elektronik, wie zum Beispiel Gehäuse, Hauben und Abdeckungen aber auch Verbindungselemente oder Werkzeuge welche bei der Arbeit an der Elektronik eingesetzt werden.
Das Material PETG-ESD besitzt eine hohe Festigkeit und gute Beständigkeit gegenüber schwachen Säuren, Ölen, Benzin und Alkoholen.
- Schlagfestigkeit von 29,8 kJ / m²
- hervorragende Bearbeitungseigenschaften, die mehrere Nachbearbeitungs-techniken wie Bohren, Schleifen, Fräsen, Gewindeschneiden usw. ermöglichen
- Eingeschränkte Temperaturbeständigkeit (>57°)
Das Material benötigt aufgrund seines niedrigeren Schmelzpunktes weniger Energie bei der Fertigung als z. B. ABS-Werkstoff. Es eignet sich besonders Konzeptmodelle aber auch den Vorrichtungsbau. Beim PLA Tough handelt es sich um eine Variante, die eine 750 % höhere Schlagfestigkeit als Standard PLA Werkstoffe besitzt.
Naphta Frei, hergestellt aus biologischen Bestandteilen!
- beständig gegen hohe Temperaturen und Abrieb
- Möglichkeit der Nachbearbeitung per CNC, Kleben und chemischen Behandlung
Das von uns verwendete ABS Plus besitzt eine erhöhte Härte, Haltbarkeit und Schlagfestigkeit.
Mittlerweile empfehlen wir unseren Kunden allerdings den Wechsel zu ASA. Das geringere Warping und der hohe UV Schutz machen dieses einfach zum besseren ABS.
Einsatzgebiete:
Gehäuse, Betriebsmittel, Vorrichtungen und Halterungen
- UV-Beständigkeit bei gleichzeitiger Beibehaltung von Dehnung und Schlagfestigkeit
- sehr gutes Oberflächenfinish
Einsatzgebiete:
elektrisch beanspruchten Teile der Unterhaltungs- oder Büroelektronik, Gehäuse, Griffe, Halterungen, Funktionsteile, Betriebsmittel
- einzigartige, holzähnliche Haptik und Optik
- 100 % aus nachwachsenden Rohstoffen
- Mechanisch und thermisch mit PLA vergleichbar
- Biologisch abbaubar nach DIN EN ISO 14855
- Wärmeformbeständig bis ca. 70 °C
Aufgrund seiner Zusammensetzung weist das Material besonders gute Eigenschaften in Hinblick auf Druckbelastung auf. Die Holzfasern lassen das Material versteifen und minimieren daher die Bruchdehnung.
- Farben schwarz oder weiß
- extrem abriebfest und nahezu unzerstörbar
- chemikalienbeständig
- extrem hohe Schichthaftung
Im Gegensatz zum SLS und MJF Verfahren bieten wir das Material in mehreren Shorehärten an. Durch die Infillgenerierung beim FDM Verfahren können in einem Bauteil unterschiedliche Härtegrade generiert werden
- 100% naturreine Rohstoffe
- Wärmeformbeständig bis 160°C
- Hervorragende mechanische Beständigkeit
- Hohe Steifigkeit und Biegefestigkeit
- Leicht flexibel für eine gute Absorbierung der Belastungen
- Sehr gute Schichthaftung
- Biologisch abbaubar nach DIN EN ISO 14855
Durch seine hohe Schichthaftung, Wärmeformbeständigkeit und Biegefestigkeit ist es nicht nur unter dem Gesichtspunkt der Nachhaltigkeit unser persönlicher Favorit.
- Kostengünstiges Verfahren insbesondere bei größeren Bauteilen
- Schnelle Lieferung von Einzelbauteilen
- sehr große Material- und Farbvielfalt
- hohe Maßhaltigkeit möglich
- mechanische Nacharbeit je nach Material problemlos
- hoher Durchsatz durch Maschinenpark gewährleistet
Farbgebung
Mechanische Bearbeitung
Technischer Hintergrund
Beim Fused Deposition Modeling (FDM) erfolgt der Aufbau der Modelle durch ein extrudiertes aufgeschmolzenes Filament auf eine Bauplattform. Das per Filamentfaden zugeführte Material wird dabei in einer Heizdüse aufgeschmolzen und das zu druckende Objekt schichtweise aufgebaut.
Je nach Größe des Objektes, Kundenwunsch oder Anforderung an den Teilepreis können flexibel unterschiedlich Schichtstärken genutzt werden. Dieser Prozess der Druckvorbereitung wird als Slicing bezeichnet. Darin werden auch alle Parameter des Druckes festgelegt, die je nach Aufbau der Modelle durchaus variieren können.
Die meisten unserer Anlagen haben geschlossene und beheizte Bauräume, damit ein Verzug der zu druckenden Teile minimiert werden kann.
Verfahrensbedingt hat die Technologie eine geringe Fertigungsgeschwindigkeit.
Neben einer fest definierten Wandstärke kann mit unterschiedlichen Fülldichten (Infill) im Modell gearbeitet werden. Das kann den Fertigungsprozess stark beschleunigen. In unserem Online Konfigurator ist es möglich verschiedene Fülldichten auszuwählen.
Überragende Geometrien stellen beim FFF Verfahren ein Problem dar. Während bei den Pulverbasierten Verfahren das nicht verfestigte Pulver als Stütze dient, muss beim FFF Verfahren eine Supportstruktur gedruckt werden. Nach der Entfernung dieser Strukturen die auch starken Einfluss auf die Fertigungszeit haben, können an den gestützten Passagen unter Umständen Irritationen auf den Oberflächen auftreten.
Der schichtweise Aufbau und die Möglichkeit den Bauprozess zu unterbrechen kann genutzt werden, um Muttern, Gewindeeinsätze und Sensorik im Druckbauteil zu platzieren.