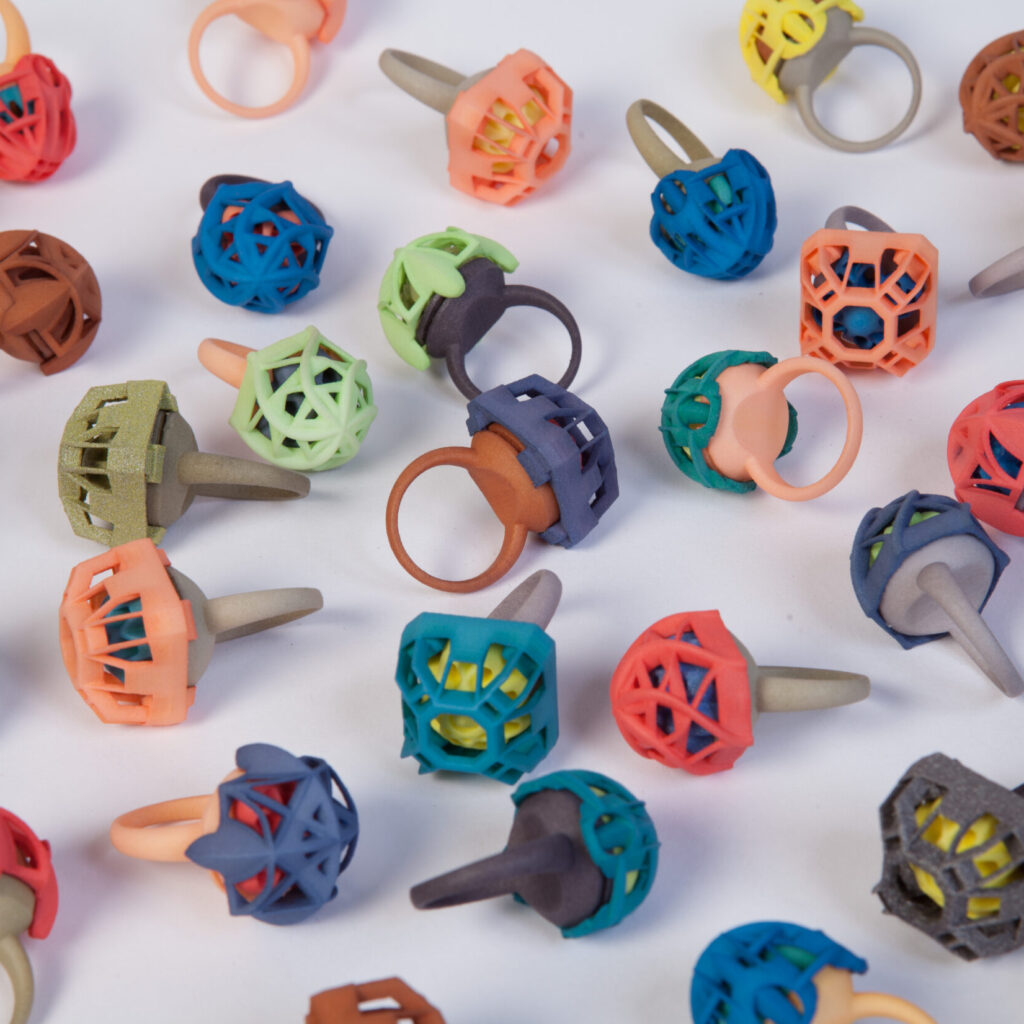
Selektives Lasersintern bei fertig+
Das Selektive Lasersintern (SLS) hat sich als Industriestandard etabliert, insbesondere für die Herstellung langlebiger und robuster Kunststoffbauteile. Das Verfahren bietet die optimale Kombination aus Qualität und Effizienz, sowohl für die Prototypenherstellung als auch für das Rapid Manufacturing.
Bei der Wahl des Selektiven Lasersinterns entscheiden Sie sich für eine bewährte Technologie, die wir mit Erfahrung und einem tiefen Verständnis für Ihre Anforderungen einsetzen, um hochwertige und funktionsfähige Bauteile herzustellen. Wir sind bereit, Ihnen mit unserem Fachwissen und unserer Unterstützung zur Seite zu stehen, um Ihre Vorstellungen erfolgreich umzusetzen.
Materialien im SLS
Beim Selektiven Lasersintern mit Kunststoff ist die Verarbeitung von verschiedenen Kunststoffen in granularer Form möglich.
- Konstruktionsfreiheit
- keine Stützstrukturen nötig
- komplexe und filigrane Geometrien
- große Bauteile
- kurze Fertigungszeiten
- Funktionale Werkstoffe
- Bewegliche Modelle können am Stück gefertigt werden
- Gute mechanische Eigenschaften
- Vielzahl an Veredelungsmöglichkeiten
- gut kalkulierbare Kosten
- Sparsamer Materialverbrauch
Qualität & Vielfalt
Unser Fokus liegt auf Qualität und Vielfalt. Wir setzen auf moderne Anlagen des renommierten Herstellers EOS GmbH, der als einer der führenden Maschinenhersteller im Bereich des Selektiven Lasersinterns gilt. Diese Geräte ermöglichen uns, präzise und zuverlässig Bauteile nach Ihren individuellen Anforderungen herzustellen.
Darüber hinaus bieten wir Ihnen eine breite Palette an Nachbehandlungsoptionen für Ihre gesinterten 3D-Drucke. Sie haben die Wahl aus verschiedenen Möglichkeiten, sei es in Bezug auf Farbgebung oder Oberflächenbehandlung.
Wir stehen bereit, um sicherzustellen, dass Ihre Bauteile nicht nur technisch einwandfrei sind, sondern auch visuell ansprechend und perfekt auf Ihre Bedürfnisse zugeschnitten.

Farbgebung
Oberflächen
Mechanische Bearbeitung
Technischer Hintergrund
Beim Selektiven Lasersintern, etabliert hat sich die Abkürzung SLS, werden 3D Drucke aus einem sehr feinkörnigen Grundmaterial generiert. In den meisten Fällen handelt es sich dabei um Polyamidwerkstoffe.
Vor dem Fertigungsprozess werden die Bauteile mittels einer Software optimal im Bauraum ausgerichtet und dieses Arrangement anschließend in einzelne Schichten entsprechend der Z-Auflösung (Schichtaufbaustärke) der Anlagen abgespeichert und übertragen.
Der Bauraum der Maschinen wird während des Bauprozesses stark aufgeheizt. Die Temperatur liegt dabei ca. 10 Grad unterhalb der Schmelztemperatur des verwendeten Materials. Mittels eines Rakels bzw. einer Dosierrolle wird kontinuierlich eine dünne Schicht Pulver aufgetragen. Wir arbeiten auf unseren Anlagen mit Schichtstärken von 0,1 und 0,12 mm. Nach dem Auftrag dieser losen Schicht Pulver gibt es eine kurze Aufheizphase. Anschließend schmilzt ein Laserstrahl selektiv die zu belichtenden Bereiche des Bauteils. Der Hotspot des Lasers beträgt dabei je nach Maschine und verbautem Laser ab 0,5 mm. Dieser „fährt“ die Konturen und Füllungen der Bauteilschicht zeilenweise ab.
Nach Abschluss dieses Einzelprozesses senkt sich die Bauplattform um die vorgegebene Schichtstärke ab und der Prozess wiederholt sich.
Dabei dient das umliegende, nicht aufgeschmolzene Kunststoff-Material als Stützmaterial. Dadurch stellen überragende Geometrien, komplexe Formen und Hohlräume kein Problem in der Fertigung dar.
Jede Belichtung einer Schicht benötigt je nach Packraumdichte ca. 30 Sekunden Fertigungszeit. Beim Beispiel einer EOS P396 mit einer Fertigungsschichtstärke von 0,12 mm dauert die Fertigung eines gefüllten Bauraums von 58 cm Höhe ca. 40 Stunden, wobei 4830 Einzelschichten belichtet werden.
Aufgrund der im Selektiven Lasersintern benötigten hohen Temperaturen muss der Baubehälter nach dem Druckprozess langsam herunterkühlen. Dieser Zeitraum entspricht ungefähr der Bauzeit des Druckjobs. Hieraus ergeben sich leider auch die größten Nachteile des Verfahrens. Bauteile am Rand des Bauraumes kühlen schneller ab als andere im Zentrum des Bauraums. Verlaufen Bauteile durch diese Abkühlzonen, kann ein Verzug des Bauteils nicht immer vermieden werden.
Nach dem Auskühlen werden die Bauteile entnommen und mittels Glasperlstrahlen gereinigt. Wichtig ist hierbei, dass sich in den Bauteilen befindliches Pulver innerhalb gewünschter Hohlräume über Öffnungen entfernen lässt. Die Bauteile können nun verwendet werden. Auf Wunsch bieten wir zusätzlich eine Reihe von Nachbearbeitungsoptionen an.